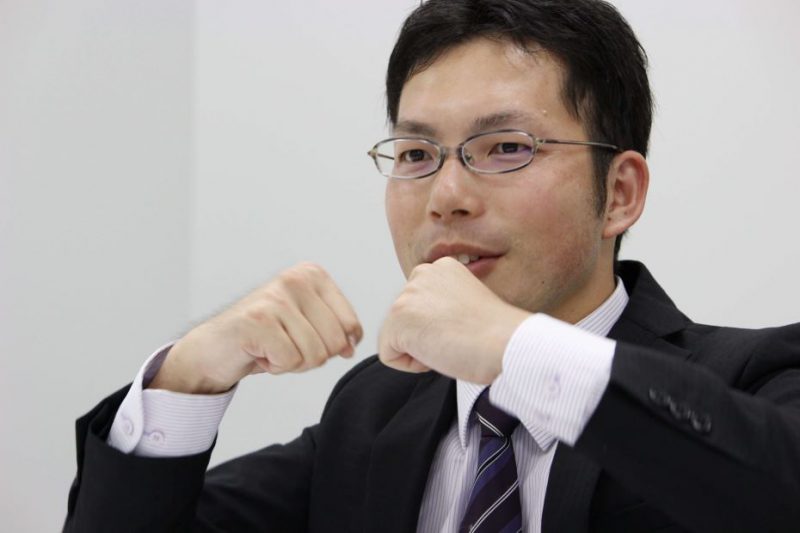
- 配信日:2020.08.06
- 更新日:2024.10.24
オープンイノベーション Open with Linkers
鉄筋自動溶接機の開発 溶接継手を普及してゼネコンの工期短縮を目指す【CB工法協会】
※本記事は、Innovation by Linkersに過去掲載した記事の再掲載記事となります。
「Linkers」でコーディネーターとして活躍されながら、今回発注者として「鉄筋自動溶接機」の開発パートナー探索をご依頼いただき、スピードマッチングにてデモ機を試作し「鉄筋EXPO2017」で公開展示を行った、一般社団法人CB工法協会の近藤 佳裕様にマッチングや製品の特長から開発経緯はもちろん、継手技術や建設業界などについて幅広く伺いました。
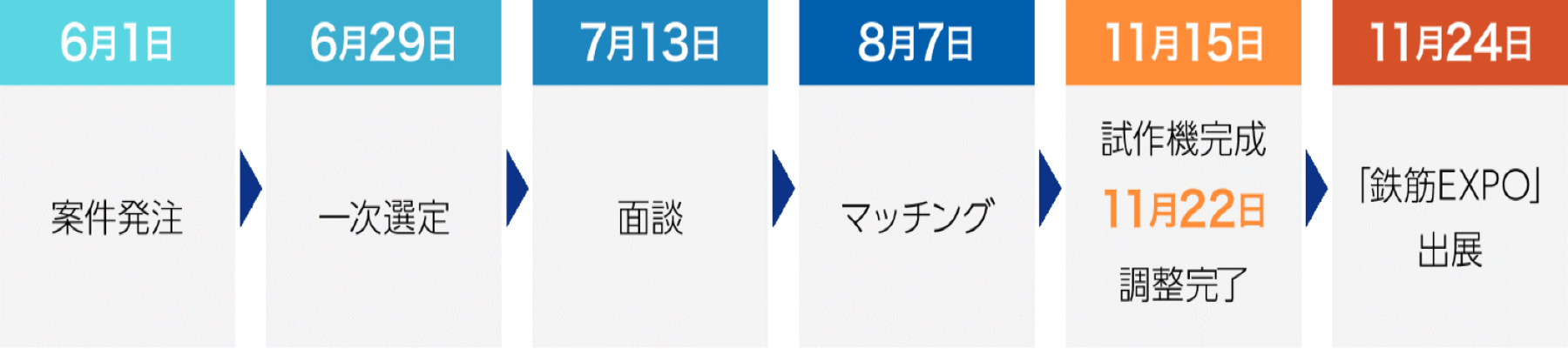
CB工法そしてCB工法協会について
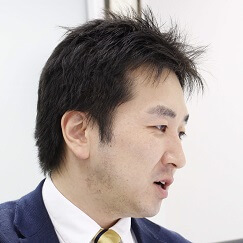
リンカーズ 尾形
CB工法についてお教えください。CB工法はどれくらい前からある技法で、CB工法協会はどのように設立されたのでしょうか?
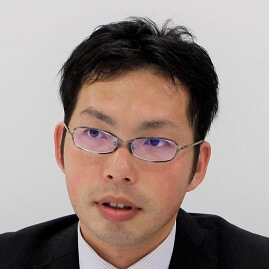
CB協会 近藤様
まず、継手(つぎて=つなげる方法)には圧接、機械式、溶接の3種類があるのですが、CB工法は溶接の1手法で、セラミックス製の裏当て材を用いて溶接をする、狭開先のエンクローズ溶接継手です。目視による溶接部の外観検査が可能な品質重視の工法です。
大阪府と愛知工業大学の共同研究・共同特許で生まれた技術で、平成元年に特許申請をしました。 現在最も普及している継手技術である「圧接」という方法は、原子間結合で繋げるのですが、分かりやすく言うと“溶かしてくっつける”です。 平成元年の頃、圧接以外に溶接継手や機械式継手も量が増えてきている中、大阪府から「より品質重視の検査のしやすい新しい継手は考えられませんか?」という経緯があって、溶接の技法である「CB工法」ができ上がりました。既存の工法も国交省などの基準で定められた数値は検査的にもちろんクリアしていますから、あとは現場での運用の話なんです。技術によるムラやミスなどなくきちんと仕上げられているかという部分に不安を感じていた大阪府から、セラミックを割って外すことでちゃんと繋がっていかどうかが目視できるという工法を評価され、平成3年に特許公開となりました。 建築業界の技術というのは基本的には1社独占が習わしなんですが、大阪府より協会を作って技術管理をして、会員みなさんが押しなべて使えるようにコントロールして下さいと言われてCB工法協会が立ち上がりました。
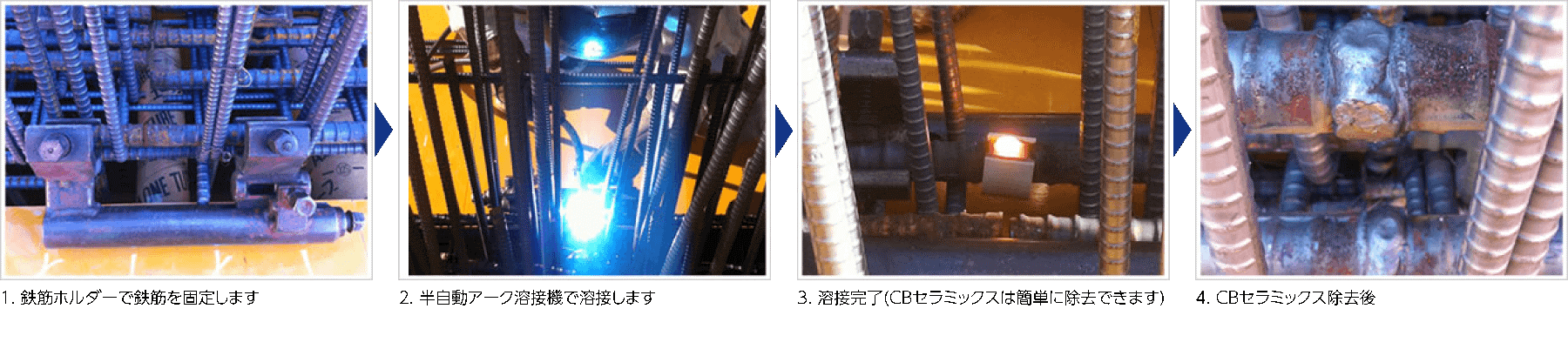
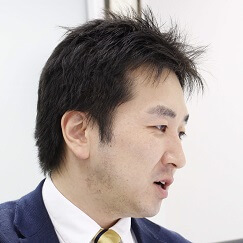
リンカーズ 尾形
なるほど。先見の明ありというところかと思うのですが、とあるゼネコン企業さんで「鉄筋自動溶接機」のお話しをしたところ、メーカーではなく協会がこの技術に特化して、しかも自動化もというところをすごく感謝されていたように感じました。今後は色んなゼネコンさんでも使われる技術になってくるのではと思いますが、CB工法はどんな建物で使われてきたのでしょうか。
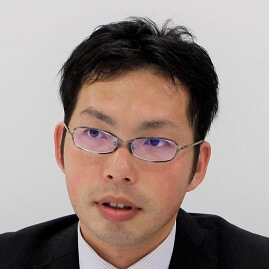
CB協会 近藤様
建築でいえばマンションやショッピングモールのような大型の駐車場があるようなところや、大きな工場や重機などが頻繁に走るような駐車場、港湾工事的に港などです。土木の分野で言えば、橋やダム、高速道路なども全部橋になりますが、基礎に鉄筋が使われているところはどこにでも使われています。東京外環道自動車道、大手運送会社倉庫、小学校など教育機関、言い始めたらきりがないですね。
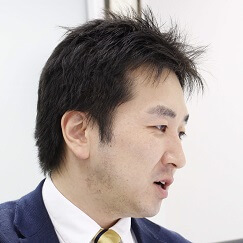
リンカーズ 尾形
始まりは大阪府からということですが、使用されているエリアに特色はありますか?
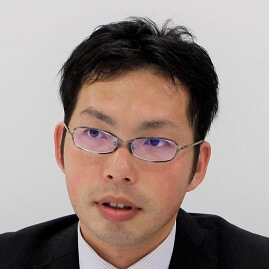
CB協会 近藤様
大阪府との共同特許で生まれたこともあって、会員さんの4割くらいは大阪なので阪神高速や新名神など、大阪の物件が多いですが、会員さんは北海道から沖縄までいらっしゃいます。継手全体のシェアでいうと大阪はかなりの部分を担っています。
継手・溶接について
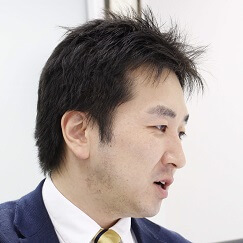
リンカーズ 尾形
現在のCB工法のシェアはどのくらいなのでしょうか?
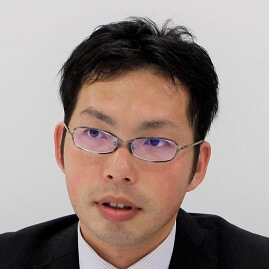
CB協会 近藤様
日本の継手業界全体で言うと約5,000万カ所あって・・・
日本の継手業界全体で言うと約5,000万カ所あって、そのうちの8割=約4,000万カ所が前述の「圧接」と呼ばれる、バーナーで炙って溶かしてくっつける工法です。残り1割=約500万カ所が「機械式」という、カバーのようなネジでカパッと包み込んでしまうような工法で、残りの1割=約500万カ所が「溶接」になります。その溶接の中の8割=約400万カ所がCB工法です。溶接の中では標準工法という形で約8割のシェアをいただいております。
各工法についてお話ししますと、圧接は国鉄時代に運輸省が作った技術です。レールをつなぐ際の鉄を溶かしてつなげる技術を用いているので、もともと建築に使うものではなかったところを流用されました。
現在、その圧接の職人さんも減ってきており、コンクリートやタイル屋さん、左官さんなど、建築に関わる分野はどこも職人さん不足です。そのため、工場で半分作ったものを組み立てるだけでマンションなどができますといった「先組み工法」や「PCコンクリート」といった工法が増えています。
しかし、圧接は溶接部分を溶かして寄せてくっつけるので、溶接する両側が動かなければならないんですね。「機械式」も同様です。そのため、コンクリートブロックが既に固まっていて動かしようのない、工場で作ってきたものを積み上げて作るには、実は溶接が向いているんです。全世界的に見ても圧接を行っているのは日本だけなんです。ガラパゴスな技術ですね。
日本含め諸外国では基本的に“経(使用する鉄筋の直径)の40倍の長さ”を重ねれば繋げなくてもいいんです。要は、鉄筋コンクリート中の両鉄筋にある程度の長さがあれば破断しない、ということなんですが、例えば51㎜の40倍だとすると 2m4㎝を重ねることになる。5㎝くらいの幅の鉄筋を使うのでコストが恐ろしく高いんです。今まで細い鉄筋を使っていた国でも段々と建物が高層化していく中で太い鉄筋を使うようになってきてその太い鉄筋を重ねていたらコストが合わないと…。
その上、単純にその長さを重ねるとすると、仮に柱だとすると、鉄筋だらけになってコンクリートの入るすき間がなくなってしまうんです。だんだんと鉄筋が太くなってきた分、重ねられずに繋がないとならない状況が、地震先進国の日本にはいち早く訪れてしまっただけなんです。
機械式も、カパッとカバーで繋げると元の鉄筋の約2倍の太さになってしまうんです。ここにグラウト剤という樹脂みたいなものを流し込んでくっつけるのですが、結局太くなってしまうので、鉄筋と鉄筋が重なっている太さと変わらないのでコンクリートも入らず、カバー自体が鉄の塊なのでコストも高いです。
台湾でも何回も地震が起きて、諸外国においてもだんだんと繋げないとならなくなってきた中で、0ベースでその技術を探し始めたとき、前述のような理由やコスト的に考えても溶接しかないと。しかも溶接の職人さんは造船だとかいろいろな分野で諸外国にもたくさんいらっしゃるんです。先日インドネシアでプレゼンしてきたときにもそのような反響を感じました。
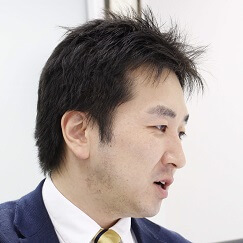
リンカーズ 尾形
溶接の伸びしろと同じくらい、CB工法が伸びてくるだろうと。
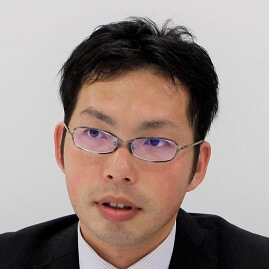
CB協会 近藤様
とは言っても日本では溶接は最大でも30%取れればというくらいだと思います。最終的には圧接・機械式・溶接が3割ずつというのが関の山かなと。どれもメリット、デメリットがありますから。
圧接は溶剤なども必要ないぶんコストが安いので、職人さんがいる限りは多分やるのではないかと思いますが、実は、圧接でも5年くらい前から自動圧接機というのができています。ただ、ジャッキを使ってジワーっと油圧でくっつけるのですが、人のコントロールでないぶん難しく、時間がかかってしまうためあまり世の中に普及しきっていないです。そして、圧接はバーナー(火)を使うので、野外の場合には雨やすごい風の日など、天候によっては施行ができません。 機械式はカバー自体にお金がかかるのですが、お金さえあれば全天候型で対応が可能なんです。カパッとはめてグラウトを剤入れるだけなので多少の雨が降っても大丈夫です。 溶接はそれらの真ん中を取っているくらいですね。

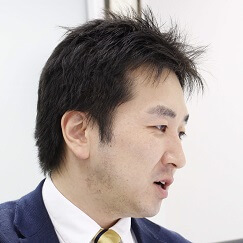
リンカーズ 尾形
強度的な違いはありますか?
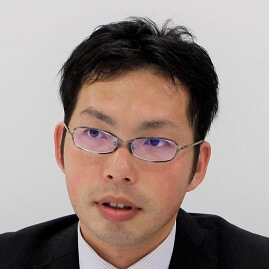
CB協会 近藤様
3工法とも国交省が出してる基準をクリアしているので、強度という意味で言えば一緒です。あとは本当に適材適所ですね。コストに起因するのか、施工状況を優先するのかなどです。
今建築の現場では工期、工期と言われているので工期短縮というのは非常に大きいです。建築現場には仮設事務所を建てるのですが、そこにはコピー機を入れたり、インターネット網や電話線なども引くので、例えば1ヵ月工期が早くなると大きく仮設費用が浮きます。そして、もしそれがマンションなどであれば、早く稼働すればそのぶんだけデベロッパー側の収入も入るので、もう本当に工期命なんです。工場で半分作って持ってきて組み立てるというのも、そういうところからも起因しているんです。
鉄筋自動溶接機について
鉄筋自動溶接機の使い方と最終商品開発に向けて
―今回発注いただいた案件である「鉄筋自動溶接機」はどのように使うのでしょう? 溶接機本体の先に、溶接トーチの代わりに自動溶接機をひとつずつセットしてスイッチを押すと施工パーツが作動します。鉄筋の固定冶具にネジが留まってるんですが、緩めたりつけたりは手動で行います。溶接する時間自体は手動の時とさほど変わらず、デモ機の35㎜サイズだと40秒ぐらいです。作業時間というよりもヒューマンリソース削減の意味合いが大きいと思います。
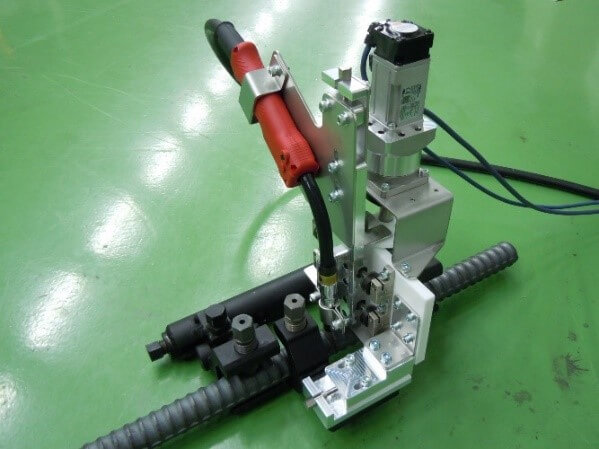
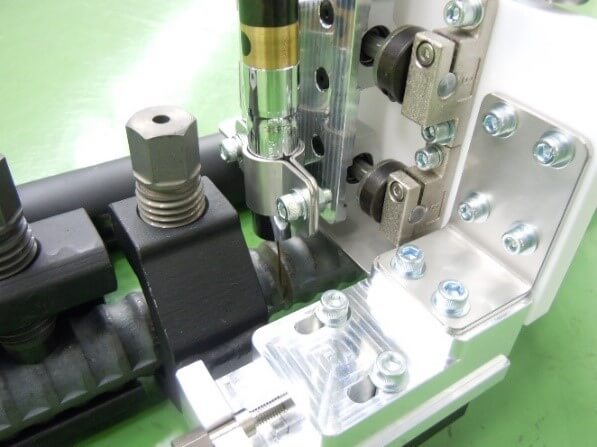
そもそもCB工法は作業工程的に“冶具とセラミックをはめる人”と“溶接する人”がセットのツーマンセルなんです。下についてる鉄の黒い部分は「鉄筋ホルダー」といって、鉄筋を繋げる時に鉄筋がズレないようにギュっと戻すための冶具なんですが、これは今でも人が一個ずつセットしています。手動で行う場合、その間にもう一人が溶接をします。自動で行う場合は、装着したら自動溶接機のボタンを押せば自動で溶接するという流れになるので、2人1組でやっていた工程が全て1人で行えるようになります。人的資源的には単純に倍の継手が稼げるようになりますね。 ―生産性が上がるということですね。打ち合わせの時に仰っていた条件は理想通りになりましたか? デモ機には既製パーツを使っていますが、今後専用のものを作り直すという前提ですので、基礎ものというか、ベースになる一号機としては十分です。「鉄筋EXPO」に向けてここまでできれば僕らの目的としてはもう十分で、先行してやっているというアピールも十分できていると思っています。 ―協会の方々の感想はいかがでしょうか? 実は機械剥き出し感レベルであれば大学生でも作れてしまうんです。ここまでは弊会でも工学部卒のスタッフが作っていたんです。最近はロボコンとか高専の人達が作るようなキットを秋葉原で買ってくれば、意外と三軸でビュンビュン動かすなんてできてしまうので、大学教授揃いの当協会内ではここまではできるよね、という空気ではありました。しかし、ここから最終商品化して一般市場に出す製品としてもっていくには大学や先生ではできないです。 それになにより弊会としては“これができていて鉄筋EXPOに出せる”ことこそが一番重要だったんです。ここから、そして、この製品から“メーカーさんにこれをやってもらう”ということが。それに、これを一緒に最終商品にしましょうねというお付き合いこそが難しいですから。 ここから“メーカーさんならではの一般市場感覚を持ち込んでの製品化”をしていただくための一発目として、すごく満足しています。スピード感も申し分なかったですし。 ―最終商品はどれくらいの期間、期限でという目標はありますか? なるべく早くというのは当然なんですが、明確には決めていないです。鉄筋EXPO用は鉄筋の直径が35㎜のサイズですが、市場には51㎜まで出回っています。この51㎜をつなげるのが実は恐ろしく難しくて、太いものをきちんと制御できるプログラムの開発に少し時間がかかるんじゃないかなと思っています。 CB工法の溶接は半自動溶接機から出ている「溶接ワイヤー」という溶接材料で鉄筋を接合します。この細いワイヤーはホースの中をずっと通っているのですが、リールに巻かれていることと、ハンドルの構造上クセがついてしまって、最後は少し曲がって出てくるんです。35㎜の細さであれば少し出ているだけなので大した湾曲にはならないですが、51㎜になるとまあまあ曲がってしまいます。物理的にこういったコントロールは必要ですが、この辺も今後改善できると思っています。またクレーター処理という過程もあり、電圧電流の調整の為に非常にたくさんの施工試験を行う必要があります。今回はあくまで“鉄筋EXPOデモンストレーション用”なので、お披露目出来たことで目標は達成です。今後は改良を重ねていきます。
溶接継手普及のためのツールなので、自動溶接機は安価で販売したい
―最初は間に合うかなと心配しておりました。 最初は無理矢理でしたからね。探索シートの中では鉄筋EXPOに出すなんて話はしていなかったので、追加課題になってしまって大丈夫かなと思っていましたが期待に応えて下さいました!! 実は鉄筋EXPOに向けては正直、担保があったんです。20年前に協会で作った機械だったらどれぐらいでできますか?と聞いたら、あのままを作るなら2週間と言われてたので、新しいバージョンでカットオーバーするのが間に合わなくても最悪それが出せるなと。でも、今回マッチングした企業のサンアローさんとしても、折角一度ものを作るのであれば次につながるもの作りたいし、カスタマイズ前提でできるだけ一発目としての“お披露目版”を作りたいと頑張ってくださいました。現時点では市場性のある重さだとかデザインといった詳細までは詰めていなくて、販売価格についてもざっくりで、15万円ぐらいで販売したいなと思っているくらいです。 ―それは安いんじゃないですか!? 非常に安いと思います。ですが、僕らは鉄筋自動溶接機を売ることが目的ではなくて、これはあくまで溶接の継手を普及させたいというパーツの一つなんです。人が行うことで精度や品質にバラつきが生じることを防ぐこともそうですし、海外では職人を教育するところから始めないとならないので、そこを短縮する為のアイテムなんです。売って儲けようっていう話ではなくて、“自動溶接機があることによって溶接で継手ができる”ということを目指しています。今後は工程特許・単純工法特許で特許も取りたいと思っています。
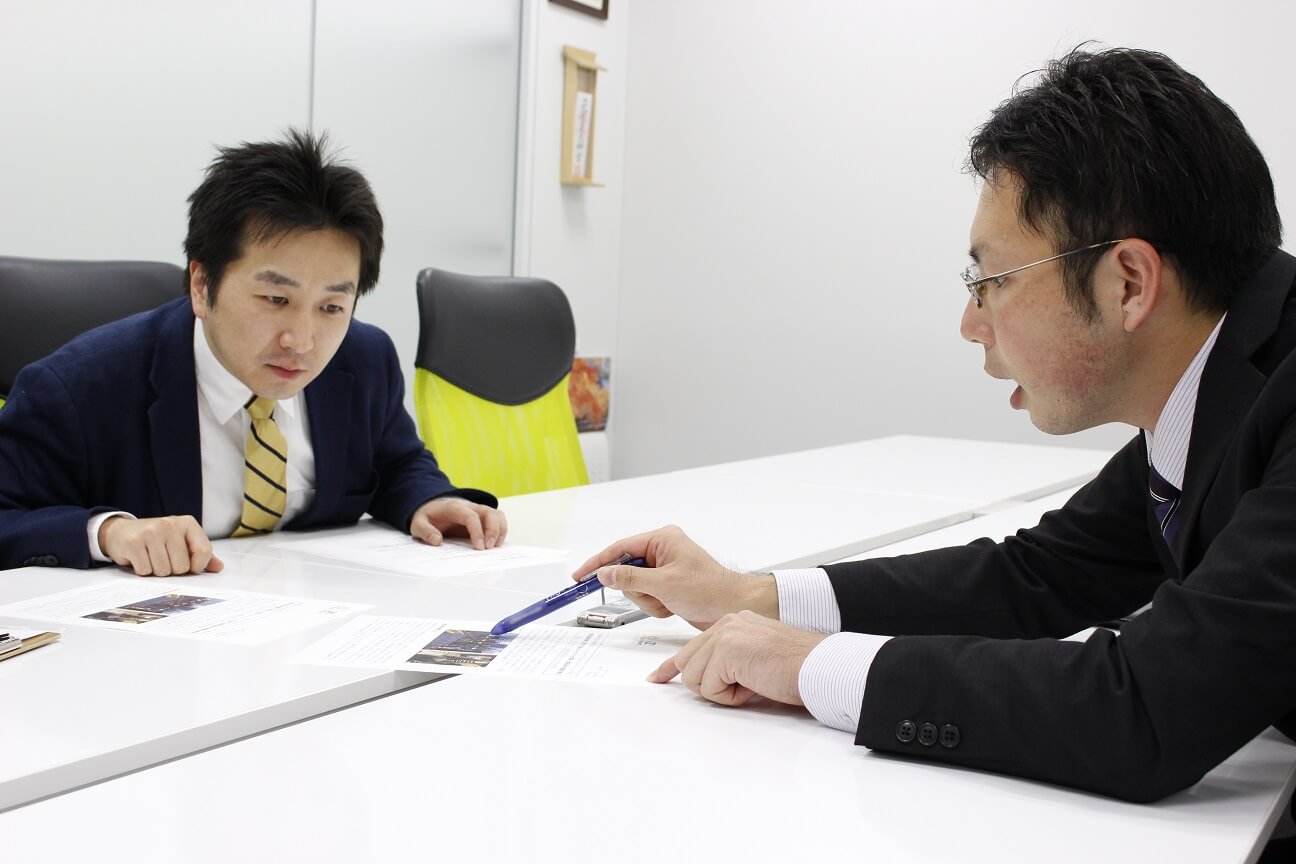
自動溶接機を広める事で、現場の設計図が溶接継手を前提としたものになれば工期短縮につながる
―この自動溶接がもっともっと認知されていけば、もしかしたら設計自体から変わっていくかもしれないと仰っていましたね。 そうなんです。現在の現場の設計図は圧接がメインで描かれていますが、現場監督さんとしては1日でも工期を早めて現場を完成させたいので、そのためには溶接を使うことを前提にした鉄筋の並べ方や準備の仕方をして、自動溶接機が活躍しやすい現場の段取りをすることが効率化に繋がります。つまり、CB工法を使いたいと希望を上げ設計図の段階から取り込んでもらえるのが現場監督さんのためにもなるんです。なので自動溶接機が広く一般的になって、これを使う前提で設計図が描かれるようになれば、すごくスムーズに物事が運ぶだろうと思います。 ―設計図が変わるというのはどういうことですか? 圧接については鉄筋が2本あったらつなぐ場所(繋ぎめ)はずらさなきゃいけないんです。互い違いにしなければいけないんですね。同一断面上にしたら全部破断して倒れてしまうのではという懸念から、並列の同じ位置に順番にポンポンとつなぐことができません。しかし溶接はずらさなくていいんですよ、まっすぐでいいんです。その為、鉄筋を置く順番や長さも均等でいいので鉄筋屋さんもいろんなパーツを揃えなくていいため、ものすごく段取りが早いです。 ―段取りもそうですし色んなものがシンプル化して、設計にも好影響をもたらしてくるであろうということですね。どれくらいで変わってくるかもしれないですか?5年とか10年とか? これはゼネコンさん次第だと思うのですが、一度CB工法を使っていただいたゼネコンさんや現場監督さんはその後ずっとCB工法を使ってくださるんです。これはきっと工期短縮という部分を評価いただいているのではと思っています。あとは現在、人がやっているため、本当にこの人は上手い人なのか?ペーパードライバーじゃないのか?といった不安感もあると思うのですが、自動溶接機になれば払拭できるので、加速度的に増えていくと思っています。 弊会としては今現在400万ヶ所くらいのところを、ここ2年~2年半くらいには500万カ所くらいにはできるのではないかなと思っています。2020年までには継手全体シェアの3割は少なからずいこうと。遅くとも100年後とまでは言わないですが、職人さんの世代交代の中で私達がおじいちゃんになる頃には多分そうなっていると思います。ですが、もし先程の目標値:全体の3割というシェアになれたとしても、2020年以降には現場の減少で、もしかしたら500万カ所と数値的には変わらなくなっているかもしれないですから、そういうことも見越して、やはり海外に出ていく必要があると思っています。 ―海外展開についてお教えください。 諸外国では継手という考え方がまだ少なく、今からなにを導入するかというだけの話なので、海外の方が展開が早そうです。現在では、現地法人化した台湾の他、インドネシアとタイが進行しています。スマトラ沖地震などありましたから、インドネシアで講演を行った際には大学の先生達からの質問がすごかったです。タイもチェンマイの中部や北部では地震があるので需要はあると思います。現在は建設現場もいろいろとボーダーレスになってきているので、ハンドリングさえできれば各国に拠点を置く必要もないかと思っています。
一般社団法人CB工法協会近藤様からの学び
技術は1社独占する事が習わしの建設業界の中で、CB工法に関しては会員皆で使う為にCB協会が設立されたという経緯。また、自動溶接機に関しては「鉄筋自動溶接機を売ることが目的ではなくて、溶接継手を普及させるためのパーツの一つ」と、言い切り「皆で使う」という趣旨からぶれない姿を見て、溶接での継手・CB工法は日本のみならず世界で主要な工法になる予感がしました。
一般社団法人CB工法協会近藤様からの学び
技術は1社独占する事が習わしの建設業界の中で、CB工法に関しては会員皆で使う為にCB協会が設立されたという経緯。また、自動溶接機に関しては「鉄筋自動溶接機を売ることが目的ではなくて、溶接継手を普及させるためのパーツの一つ」と、言い切り「皆で使う」という趣旨からぶれない姿を見て、溶接での継手・CB工法は日本のみならず世界で主要な工法になる予感がしました。
人気のタグ